No, what he has is a very useful machine and an excellent hobby. A 2500lb gehl vs a stupidly heavy 5500 lbs 763f. Give me the small, nimble gehl any day and I don't need a 1 ton dually truck to haul it. You can keep the fuel sucking, sod destroying, stupidly expensive to repair 763f monster. Keep up the excellent work I can't wait to see it done and working.
I totally agree that I bought a money pit. The thing is, I knew that before I bought it but I got it anyway because 1) I haven't worked much with these types of machines before and I wanted to learn more so I figured it is tuition 2) I wanted a smaller machine not only because of the intended use once it's finished, but while working on it the space it invades would be much less than a full size machine. It needed more done to it than I thought or hoped - let's face it, the thing was beat to a pulp - but it is coming along and will turn out fine in the end.
After working on it for so long now and learning it inside & out, I have to disagree that it is junk (in terms of
design rather than condition). Sure there are much better, slicker machines out there but not for the price I paid for this one. The short time that I got to use it before taking it apart, it proved to be more powerful than I thought it would be. I think no matter what you have you'll wish you had something bigger, but the hydraulics, while kind of slow, are enough to tear itself up if you kept at it. The drive is hydrostatic which I would prefer over the small Bobcat variable belt drive small machines (for example), plus I discovered that it shares the same Sundstrand hydrostat used in several small John Deer machines (mowers) making used parts pretty easy to find, which was a pleasant surprise. This drive is robust too, evident in the condition of it after 40+ years of probably negligent use and showing only minor, easy-to-recondition wear.
I have a 1-acre lot and
for my purposes a large skidsteer would be under-utilized. I will be doing some amount of moving dirt and digging, but the speed at which I do it is not so important as for a guy using one for profit. It's all just for my own personal use and a lot of that will be just using forks to move heavy stuff from place to place and a tiny skidsteer like this is a
great fit.
So anyway, that's why I've picked this project rather than another. With a bit of luck, I could have possibly spent the same amount and ended up with a more powerful machine. So I think the question is not whether what I'll end up with is less powerful or less valuable than something else, but what arguments could be made where this little thing is preferable to a 763 or the like. No one thing would be enough to be worth the difference, but totaling up the preferable differences, again
for my purposes, makes this little Gehl win out over other machines. The simplicity and cost of the much smaller and simpler engine, pump, hydrostats, cylinders, fuel, etc. is appealing to me. Since I won't be using it professionally, keeping the maintenance costs for my machine this low are quite appealing. The weight means I can tow it with my F150 pretty easily. I won't be hauling it that often, but I'm pretty much already "tooled up" to do so when those times come up. The trailer alone heavy enough to haul a big skidsteer costs more than I have into this machine so far. The small size means I can fit it with a bucket into my garage along with my mower in a single bay, and I'm not positive yet but I think the hoe attachment can even be shoehorned in there as well.
So on to new things. Here's the picture of the installed bracket:
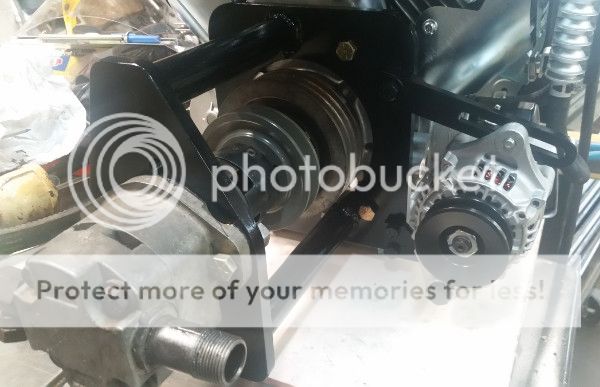
Since that is complete, I thought it time to turn attention back to getting the hydrostats put back together. I forgot that there were two bearings still needing to be removed for replacement. This is because I needed an internal puller to get them out. I didn't already have one, so I whipped one up and it worked fine.
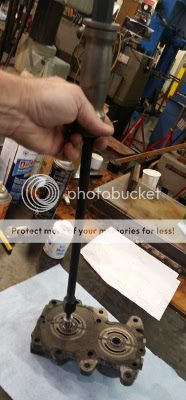
And then the bearings were out:
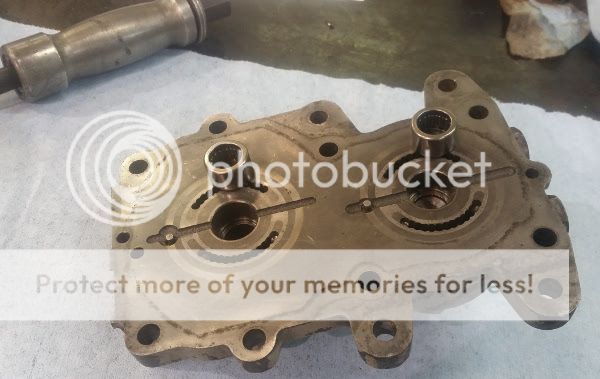
So that's the update of the day. And by the way, thanks for the compliment. I don't think anyone has ever told me "I got game" hehe. I like it.