vinito
Well-known member
- Joined
- Nov 19, 2015
- Messages
- 199
By the way, when I start this thing up the first time, it will be blocked up so the tires are off the ground. Seems safer and prudent in case something goes goofy.Wheels-on does look pretty cool. I punted the paint down the road though figuring it won't take long to do, I can do one at a time if I wish, and shortens the path to a functioning machine. So wheels are white, but installed and rolling. It's inspiring.
Today I finished the alternator mount. I'll post a picture once I get one. This means I can now install the motor, alternator and hydraulic pump permanently. More permanent assembly!!
Gear box rebuild kits arrived today so I hope to have those finished tomorrow. If so, then they can also be installed though I'll have to leave it a little wiggly so once the hydrostats are installed I can line up the shafts right, which might take a little shifting of the gearboxes.
"THen when you get to the end, you hope it's all correct at startup." ... yea well I'm kind of counting on it not being right on that day just because of the way things have been going. But I've also been trying to be super diligent and pay attention so whatever may be wrong is likely to be fairly minor. I'd like to be optimistic about everything working right off the top, and I guess I am a little bit, but there sure is a lot of things that need to be right. I can say that one thing I hope to have right from the start is simply to have no leaks. That would be fantastic. I may have just jinxed myself there though, hehe.
Well I have a couple pics. First is the bracket installed without the alternator blocking the view of how it's made. Starting from scratch I probably would have designed it different, but I had a few parts already and was able to just alter and shift them around a little to make it work.
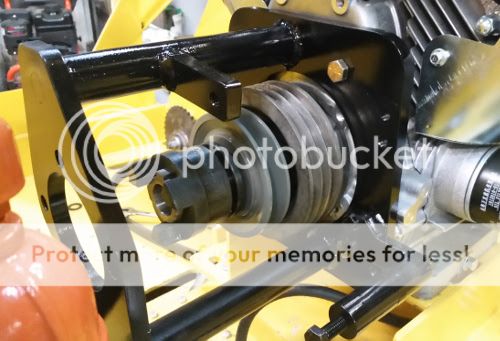
Here is the alternator installed. I tried to wiggle it around and I tell ya, it's solid as a rock.
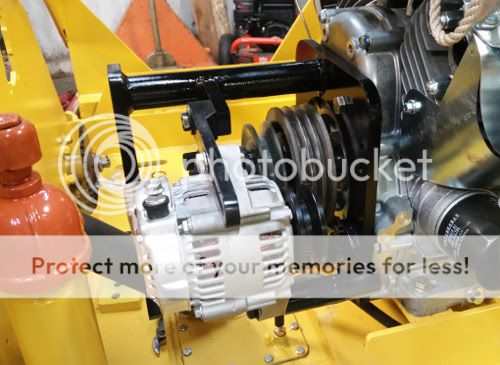
And just for fun, here's a peek at the machine with the wheels on. Holy cow! It's kinda starting to look like a machine - or a dune buggy er sumthin' anyway.