TheCoalMiner
New member
- Joined
- Oct 17, 2020
- Messages
- 1
I'm so mad right now.. Glad the wife is at work. lol.
So i recently bought a 2005 john deere ct322.
It came with a bush hog that USE to be a boom mower. ( Alamo )
When I bought it.. the original owner said "oohh yea it cuts great " yet I noticed both the ends of the case drain were plugged. I thought to myself at 1st glance.. Not for long and Just after he showed me it worked.. He hit reverse on the PTO and the case of the pump had a catastrophic failure lol. Ive seen similar set ups like this before and the case drains every time it stops. There has to be a relief valve for the case.
So I got 2k off the machine. lol.
So i took it home and pulled the pump off the mower deck and took it to a local shop for repair. they called me and said no dice.. not repairable and i should come in and look at it.. it literally exploded inside the case..
I paid 2880 thinking it cheaper then a new hog so hell with it.. New pump and I'm rolling. I waited almost a month for the pump to come in. But once it did.. I mounted it and it ran great..It got dark so I just took a run up and back on the father in laws property. 5-8 minutes of run time..
So today I go and hook it up again. Ran great then stopped running entirely.
so i raised the boom and locked it to get out and see what was going on I bumped the pto getting out and boom it exploded. Unreal.
I know I reversed the flow into the case causing it to fail. But im wondering.
How can I stop that from happening? Like a check valve not allowing pressure to backflow?
its a 1 inch JIC. Here's pics.
1st case
the one that exploded today......
you can see i ran a 1 inch line from the case drain.. i needed a check to stop the flow of fluid from going back into the pump case.
https://photobucket.com/u/dague2007/p/bcc38f2d-74ec-44c0-b69f-8388934cfe48
https://photobucket.com/u/dague2007/p/d4843e0b-0c27-4afe-b036-53fbee220e6e
https://photobucket.com/u/dague2007/p/3c6aa1a1-9dbc-42c9-a3a4-c12b57c35707
https://photobucket.com/u/dague2007/p/fd783db8-bb9b-4afb-88d9-93ecced2cc1a
So i recently bought a 2005 john deere ct322.
It came with a bush hog that USE to be a boom mower. ( Alamo )
When I bought it.. the original owner said "oohh yea it cuts great " yet I noticed both the ends of the case drain were plugged. I thought to myself at 1st glance.. Not for long and Just after he showed me it worked.. He hit reverse on the PTO and the case of the pump had a catastrophic failure lol. Ive seen similar set ups like this before and the case drains every time it stops. There has to be a relief valve for the case.
So I got 2k off the machine. lol.
So i took it home and pulled the pump off the mower deck and took it to a local shop for repair. they called me and said no dice.. not repairable and i should come in and look at it.. it literally exploded inside the case..
I paid 2880 thinking it cheaper then a new hog so hell with it.. New pump and I'm rolling. I waited almost a month for the pump to come in. But once it did.. I mounted it and it ran great..It got dark so I just took a run up and back on the father in laws property. 5-8 minutes of run time..
So today I go and hook it up again. Ran great then stopped running entirely.
so i raised the boom and locked it to get out and see what was going on I bumped the pto getting out and boom it exploded. Unreal.
I know I reversed the flow into the case causing it to fail. But im wondering.
How can I stop that from happening? Like a check valve not allowing pressure to backflow?
its a 1 inch JIC. Here's pics.
1st case

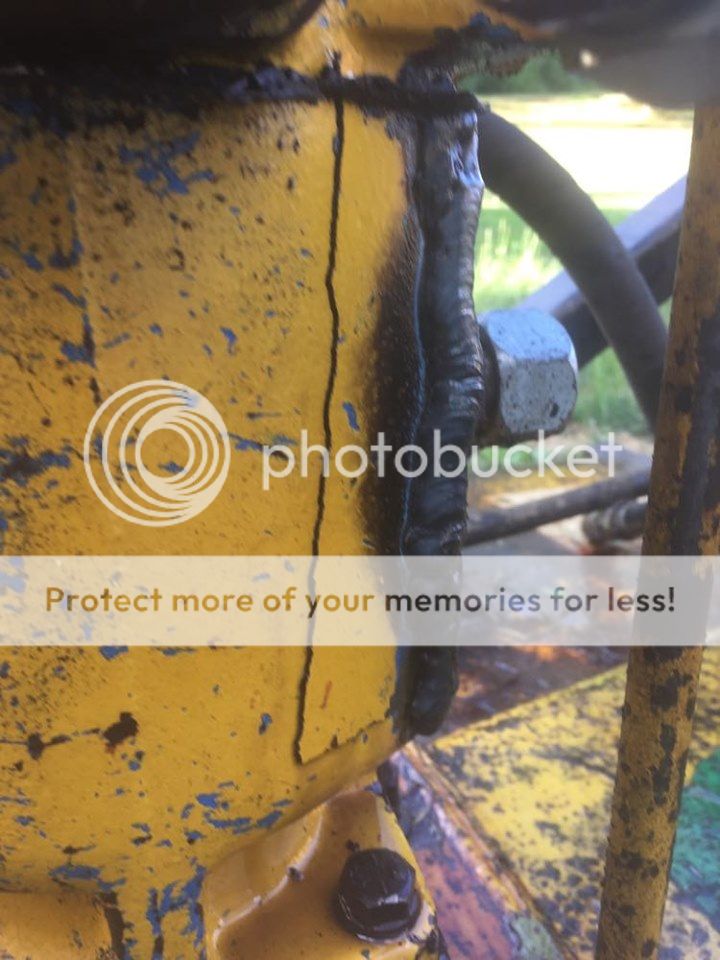
the one that exploded today......
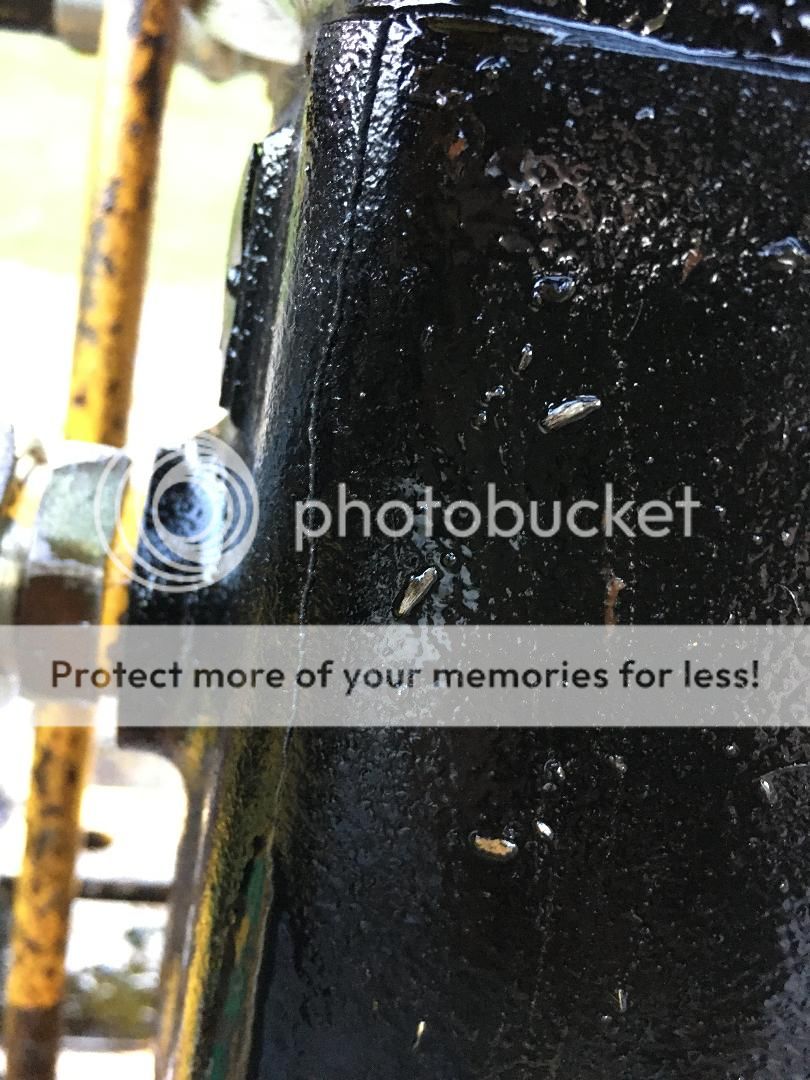
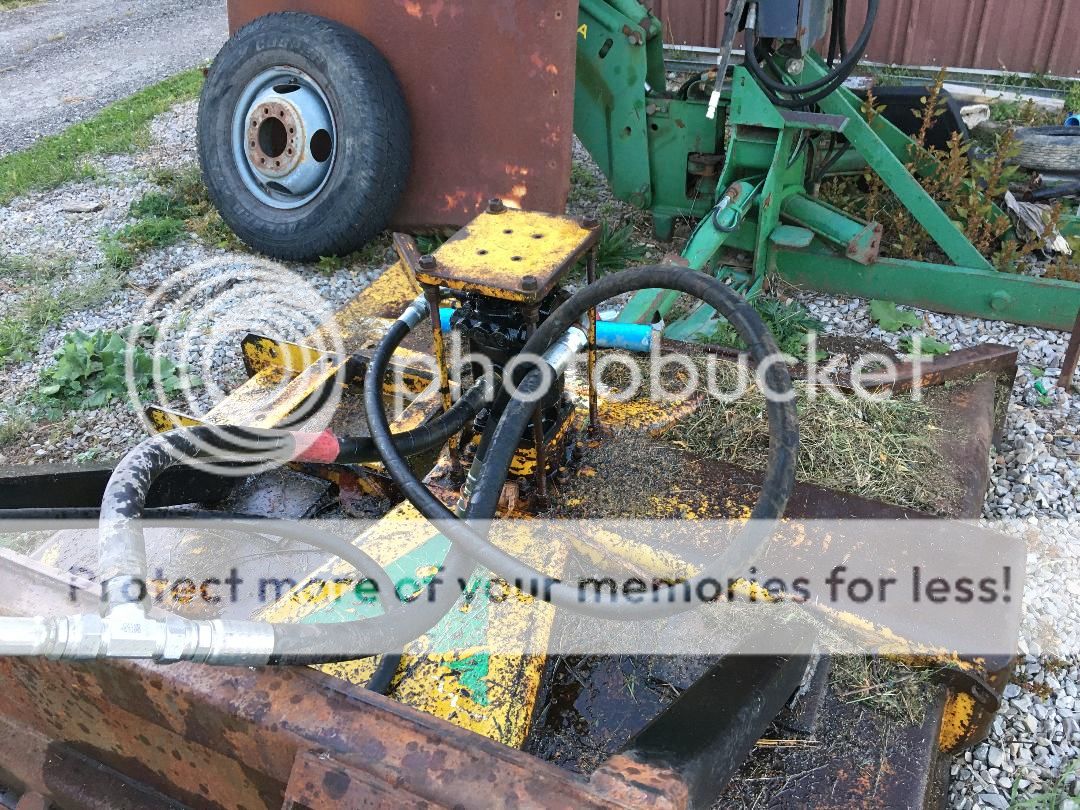
you can see i ran a 1 inch line from the case drain.. i needed a check to stop the flow of fluid from going back into the pump case.
https://photobucket.com/u/dague2007/p/bcc38f2d-74ec-44c0-b69f-8388934cfe48
https://photobucket.com/u/dague2007/p/d4843e0b-0c27-4afe-b036-53fbee220e6e
https://photobucket.com/u/dague2007/p/3c6aa1a1-9dbc-42c9-a3a4-c12b57c35707
https://photobucket.com/u/dague2007/p/fd783db8-bb9b-4afb-88d9-93ecced2cc1a