alchemysa
Well-known member
- Joined
- Mar 29, 2016
- Messages
- 203
As mentioned in a previous thread my 610 'project' had no operating variable sheave system and had simply been permanently fixed at a slow ground speed thanks to a chunk of pipe shoved into the piston.
I'm not likely to find a replacement hydraulic sheave system at a reasonable price in the near future so I've come up with this assembly that lets me fairly easily alter the speed while the engine is switched off. I must admit I have only run this in the workshop so far but it seems to work OK. It could be refined for sure but I need to get some other things sorted out before I can really give it a workout.
A heavy duty spring mounted on the outside of the sheave applies pressure which then forces the belt to move to either a larger diameter (higher ground speed), or allows it to shrink to a smaller diameter (lower ground speed). Basically its a manually operated version of the spring loaded 'driven sheave' thats at the other end of the belt. Its necessary to stop and start the engine about 3 times in order to go from one extreme to the other. Its not perfect but I should be able to find a setting that suits me for most jobs around my block and I'll still have the option of a higher speed if I really do have to travel some distance.
Total cost in parts was about $30. The pics here show the basic setup but note that a couple of things changed along the way. The final assembly used a longer bolt and had a much heavier spring. (In fact it has two springs, one inside the other, as can just be seen in the last pic). The thing is that this spring assembly has to be stronger than the big spring on the driven sheave or it wont work. I was lucky enough to find a spring maker in town who had boxes of oddments so I was able to get a half dozen assorted springs for $10.
The other tricky bit to track down was the piece of brass bar. Its 1-7/8" (47.63mm) diameter and fits inside the sheave perfectly. In fact I think its the size that the original gland inside the sheave is machined from. Although its a stock size its not really common. A metal merchant put me onto an engineering place that had a few offcuts lying around. This bit cost me $20 and they lathed a hole through the middle to take the M12 metric bolt. The length of the bar isn't critical. This one is about 2"
If anyone wants any more details sing out. But for now I have a question. Can someone please tell me the distance from the outer edge of the drive sheave to the belt when the belt is in the high and low speed positions? At the moment I don't know how much 'travel' between high and low is ideal. I hope that makes sense.
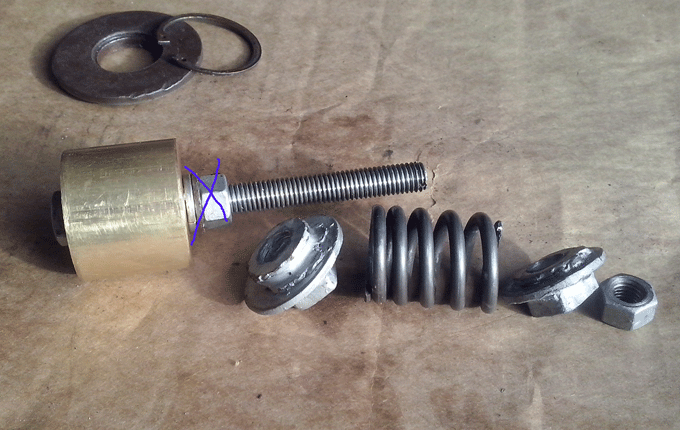
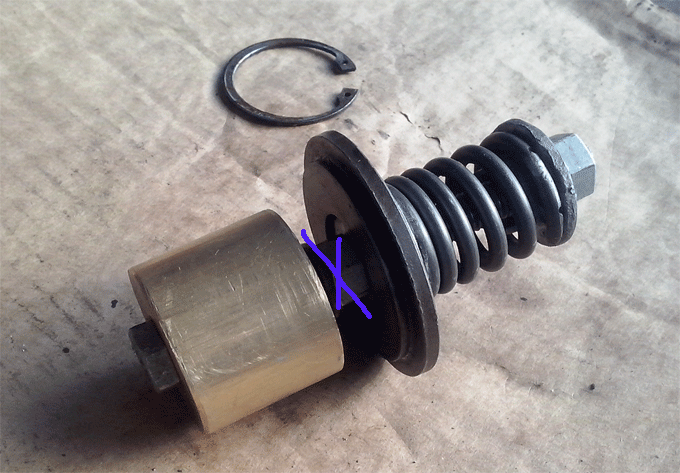
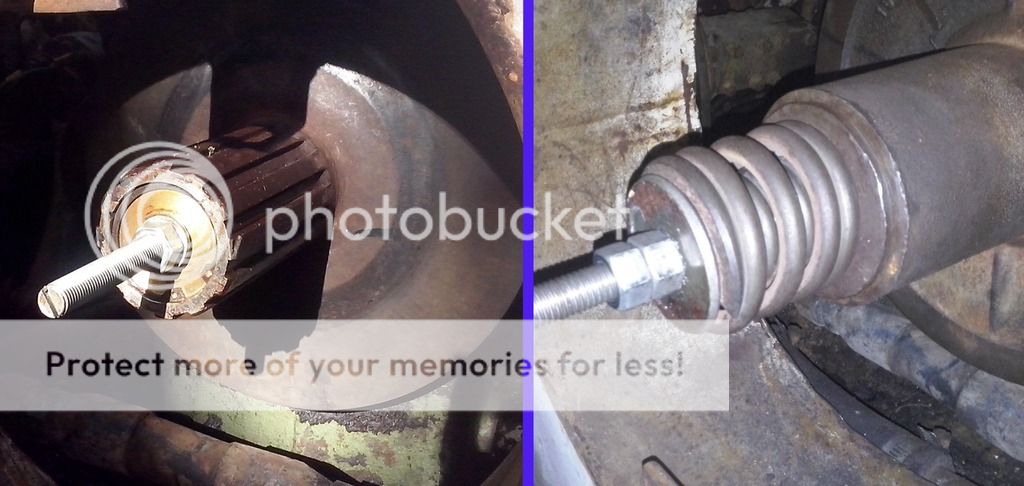
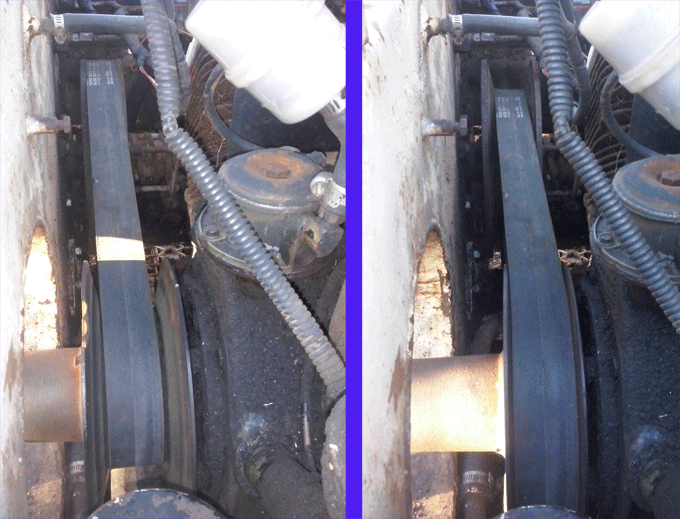
I'm not likely to find a replacement hydraulic sheave system at a reasonable price in the near future so I've come up with this assembly that lets me fairly easily alter the speed while the engine is switched off. I must admit I have only run this in the workshop so far but it seems to work OK. It could be refined for sure but I need to get some other things sorted out before I can really give it a workout.
A heavy duty spring mounted on the outside of the sheave applies pressure which then forces the belt to move to either a larger diameter (higher ground speed), or allows it to shrink to a smaller diameter (lower ground speed). Basically its a manually operated version of the spring loaded 'driven sheave' thats at the other end of the belt. Its necessary to stop and start the engine about 3 times in order to go from one extreme to the other. Its not perfect but I should be able to find a setting that suits me for most jobs around my block and I'll still have the option of a higher speed if I really do have to travel some distance.
Total cost in parts was about $30. The pics here show the basic setup but note that a couple of things changed along the way. The final assembly used a longer bolt and had a much heavier spring. (In fact it has two springs, one inside the other, as can just be seen in the last pic). The thing is that this spring assembly has to be stronger than the big spring on the driven sheave or it wont work. I was lucky enough to find a spring maker in town who had boxes of oddments so I was able to get a half dozen assorted springs for $10.
The other tricky bit to track down was the piece of brass bar. Its 1-7/8" (47.63mm) diameter and fits inside the sheave perfectly. In fact I think its the size that the original gland inside the sheave is machined from. Although its a stock size its not really common. A metal merchant put me onto an engineering place that had a few offcuts lying around. This bit cost me $20 and they lathed a hole through the middle to take the M12 metric bolt. The length of the bar isn't critical. This one is about 2"
If anyone wants any more details sing out. But for now I have a question. Can someone please tell me the distance from the outer edge of the drive sheave to the belt when the belt is in the high and low speed positions? At the moment I don't know how much 'travel' between high and low is ideal. I hope that makes sense.
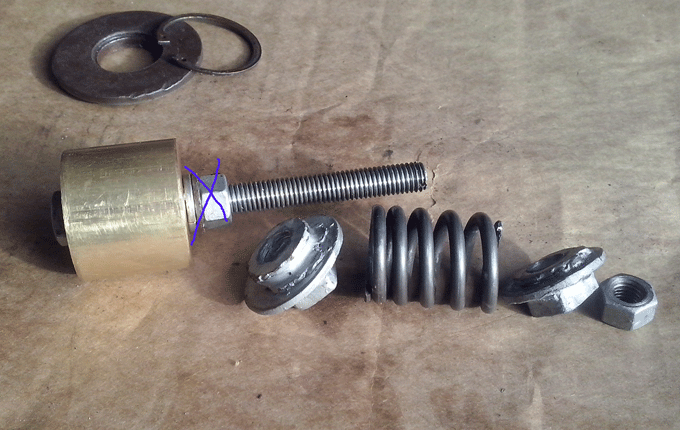
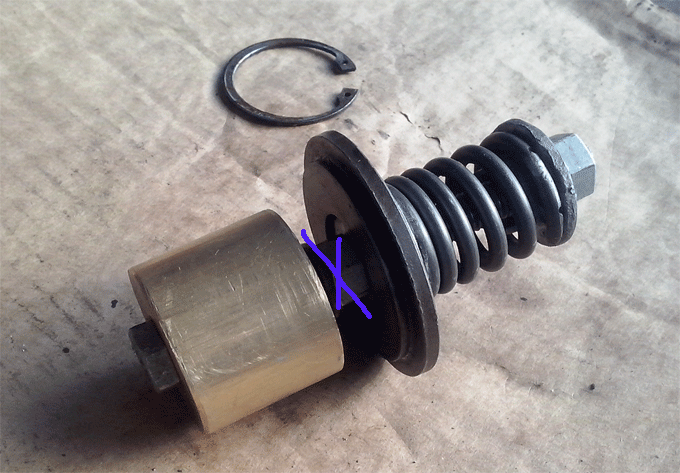
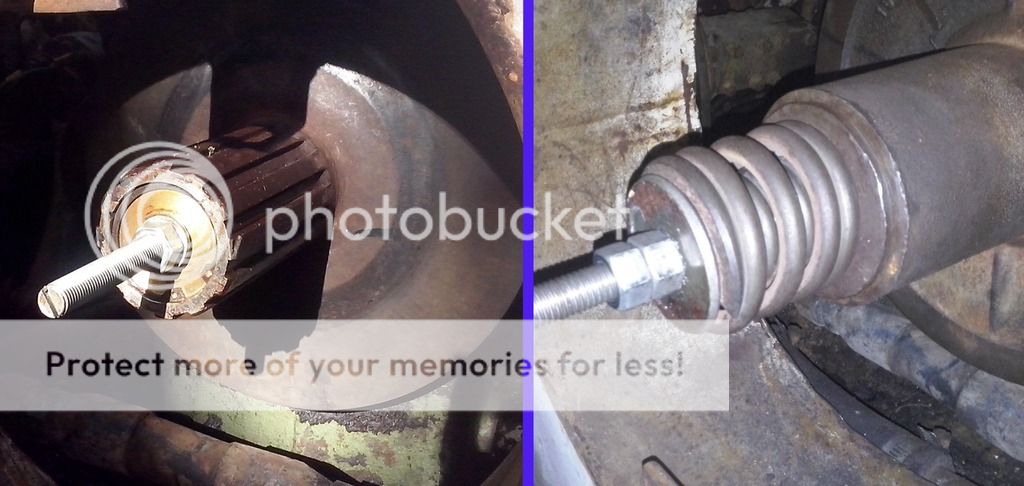
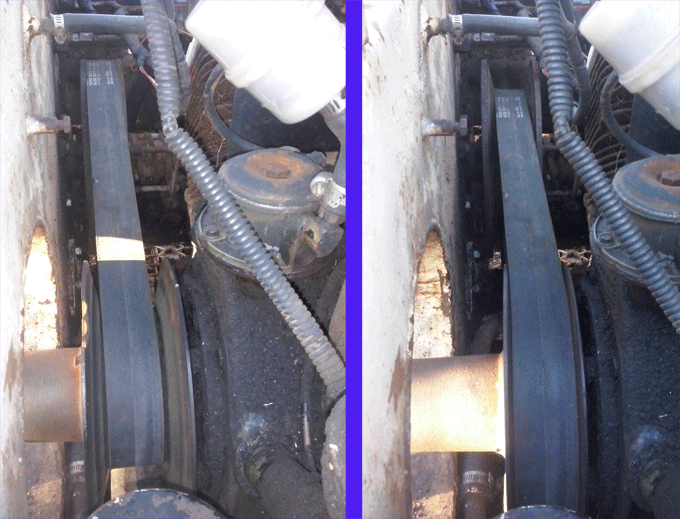