Ok, got a flywheel and had to take it in to be resurfaced. Where the clutch disc rides is actually raised above the face of the flywheel about .035" or so, so it creates a step. Can't have that. So I had them grind it completely flat. Total cost of flywheel and grinding, $90. Not too bad I guess. Next I had to make a stepped plug to fit the flwheel and the drive plate. I did this on my small lathe, Though about doing it on the ancient beast in the pole barn, but it has a 4 jaw and my little 9x has a 3 jaw chuck which is much easier. Anyway, you can see by the pics what I had to do. The plug fits the flywheel and the drive plate very, very snug. Had to oil it to get them both on. I drove the cutter into the base of each step for relief. In the pic they look like they are radiused, but there is actually a relief there. I also faced the base off where the back of the flywheel will rest. This makes everything square.Make sure you take lots of pictures! sounds like a good project.
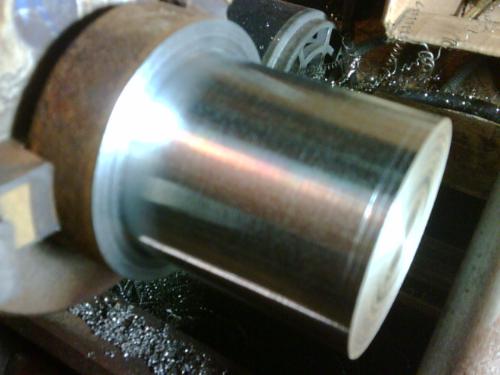
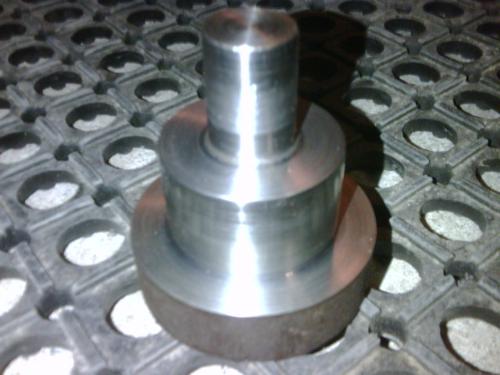
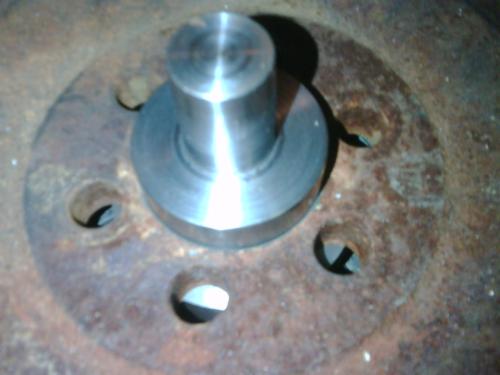
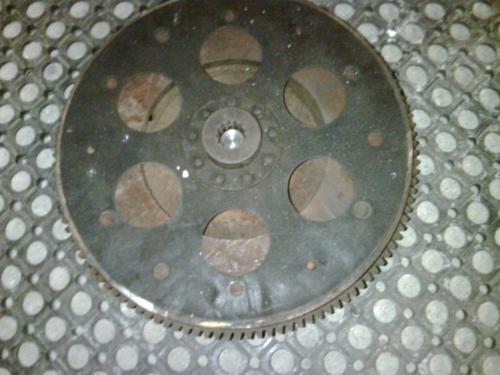
Had to drill and tap the bolt holes for the drive plate next. They are the 5/16-18's that came off the Ford flywheel. Ticks me off, cuz I had a 15" Troyke rotary table for 8 years, used it maybe twice, sold it last week, now I could use it. Oh well. just makes things take a little longer. Anywho, center punched all six holes with the drive plate clamped to the flywheel and my plug in place to make sure all is lined up. Drilled them on the mill, then put a transfer punch in the collet and used that in the recess in the back of the tap to keep the tap straight. Turned the tap with a wrench, using very slight down pressure on the quill to get the tap started enough it wouldn't wander. Then finished tapping by hand. Kind of tedious, but it got the job done. There you have it. 1 drive plate mounted to a Toyota 20r flywheel. I left out all the boring stuff, like setting it up on the mill, dialing things in, etc... Things you have to do when machining just about anything. You get the idea though. So with all this, from the back of the motor to the tailend of the drive plate hub on the Toyota, it is about 1/4" shorter than it was with the Ford. This will still leave me with 1-1/8" of pump input shaft in the drive plate (vs. 1-3/8"). I don't think that will be an issue, but if anyone else thinks or knows different, please speak up. Last thing I want to do is twist the pump shaft off. That'd be bad.
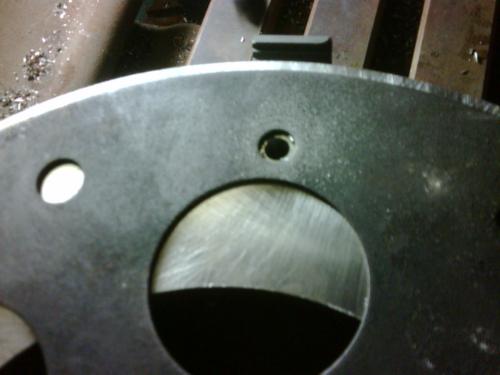
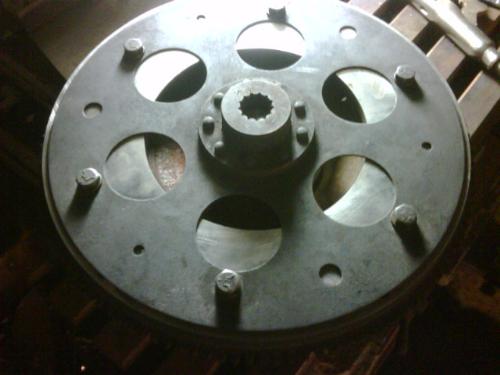
I changed my mind about making a new "bell housing". I'm just going to modify the existing one to fit the Toyota engine. I did more measuring and checking, and making one from scratch is really not necessary. I'd just be making more work for myself in the long run I think. But I'll keep updating this as I make progress. So far so good though.......enjoy!