peebeeaitch
Well-known member
- Joined
- Dec 3, 2012
- Messages
- 115
So I got going on a new project for the little machine the other day.
In my Prestolite post there is a mention of those infuriating control valve spools. My machine was stuck on the driveway for the entire winter of one of the four coldest winters in Illinois history. The cause was a combination of frustration, ignorance, haste, incompetence and misplaced enthusiasm. The eventual restarting of the machine had much to do with this forum.
Then, to add insult to injury, a colleague offered to move a very heavy piece of equipment I purchased with his Cat 263B. After doing the difficult stuff, he "suggested" I move the machine back to the trailer for him. When I'd secured myself inside he nonchalantly told me that once I had used the electronic controls I would never be able to use my machine again.
He was partly correct. The side sticks are really cool. I have plenty of slop in my foot pedals, and the control is anything but. More of a digital raise/lower at fastest possible rate. There is a bit of bind between the left and right yankem which results in me being able to drive in a straight line with my left hand on the left stick and my right holding a beverage.
I was insulted so I started shopping around for proportional hydraulic valves. Wow. Was I brought down to earth quickly: there are the quality devices (things one would trust with one's life, or fortune), one step down the stuff that doesn't have the name, but looks the same, and then the stuff which looks the same but costs 1/10th. And the 1/10th was 10x more than the budget.
So late one night I came up with the (hopefully) brainwave of using my existing control valves, but adding digital control to them using radio control servo valves. This is the second version of the servo box for the arm functions:
For those interested, the idea is to use a RC servo control board, coupled to PSP style thumb sticks and RC high torque servos to manipulate the aux and motor mechanical actuators.
The RC servo control board is this one:
(From the Pololu.com website)
Basically, this little thing outputs a RC servo command based on either direct computer input, or some manipulated electronic input.
So here are the steel parts as received from the laser, plus test fitting the servos:
This photo includes the thumb controllers:
Ok, so I dawdled off to the office to TIG in the various nuts and tap the various holes:
I spent a lot of time finding models for the servos to plonk into my box model. Unfortunately for me, I spent less time on the servo arm models and thought that my approximation of their size would do.
Assumption is the mother of all f ups, so this is the result of the assumption:
I have a couple of options to get the push/pull rods to be centered in the slots, but it is not looking good for a generic solution.
In my defense, this whole thing is designed to be able to fit into the space of the manual control arms and require zero modifications the little machine, except drilling of some holes.
Don't expect regular updates on this post. This is going to require quite a lot of experimentation and trial and error, but the purpose of posting was to encourage my progress,
In my Prestolite post there is a mention of those infuriating control valve spools. My machine was stuck on the driveway for the entire winter of one of the four coldest winters in Illinois history. The cause was a combination of frustration, ignorance, haste, incompetence and misplaced enthusiasm. The eventual restarting of the machine had much to do with this forum.
Then, to add insult to injury, a colleague offered to move a very heavy piece of equipment I purchased with his Cat 263B. After doing the difficult stuff, he "suggested" I move the machine back to the trailer for him. When I'd secured myself inside he nonchalantly told me that once I had used the electronic controls I would never be able to use my machine again.
He was partly correct. The side sticks are really cool. I have plenty of slop in my foot pedals, and the control is anything but. More of a digital raise/lower at fastest possible rate. There is a bit of bind between the left and right yankem which results in me being able to drive in a straight line with my left hand on the left stick and my right holding a beverage.
I was insulted so I started shopping around for proportional hydraulic valves. Wow. Was I brought down to earth quickly: there are the quality devices (things one would trust with one's life, or fortune), one step down the stuff that doesn't have the name, but looks the same, and then the stuff which looks the same but costs 1/10th. And the 1/10th was 10x more than the budget.
So late one night I came up with the (hopefully) brainwave of using my existing control valves, but adding digital control to them using radio control servo valves. This is the second version of the servo box for the arm functions:
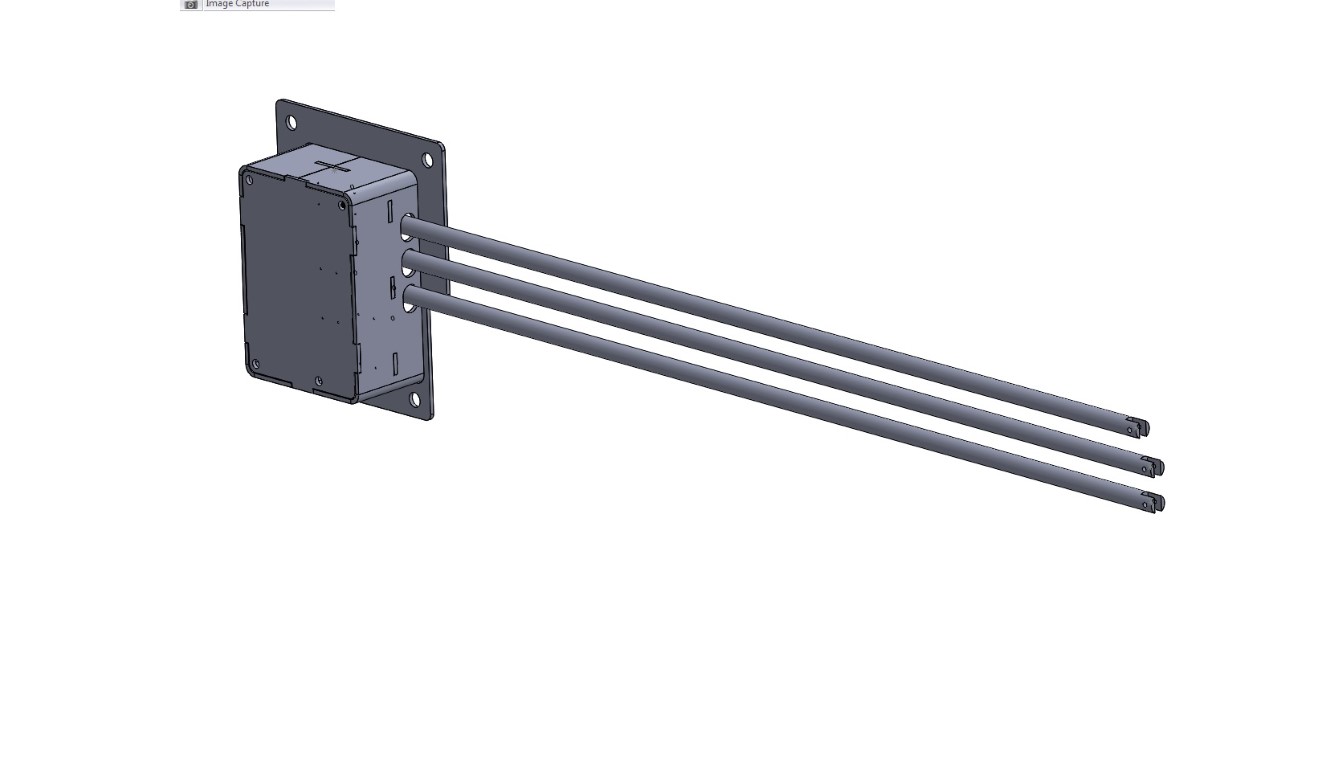

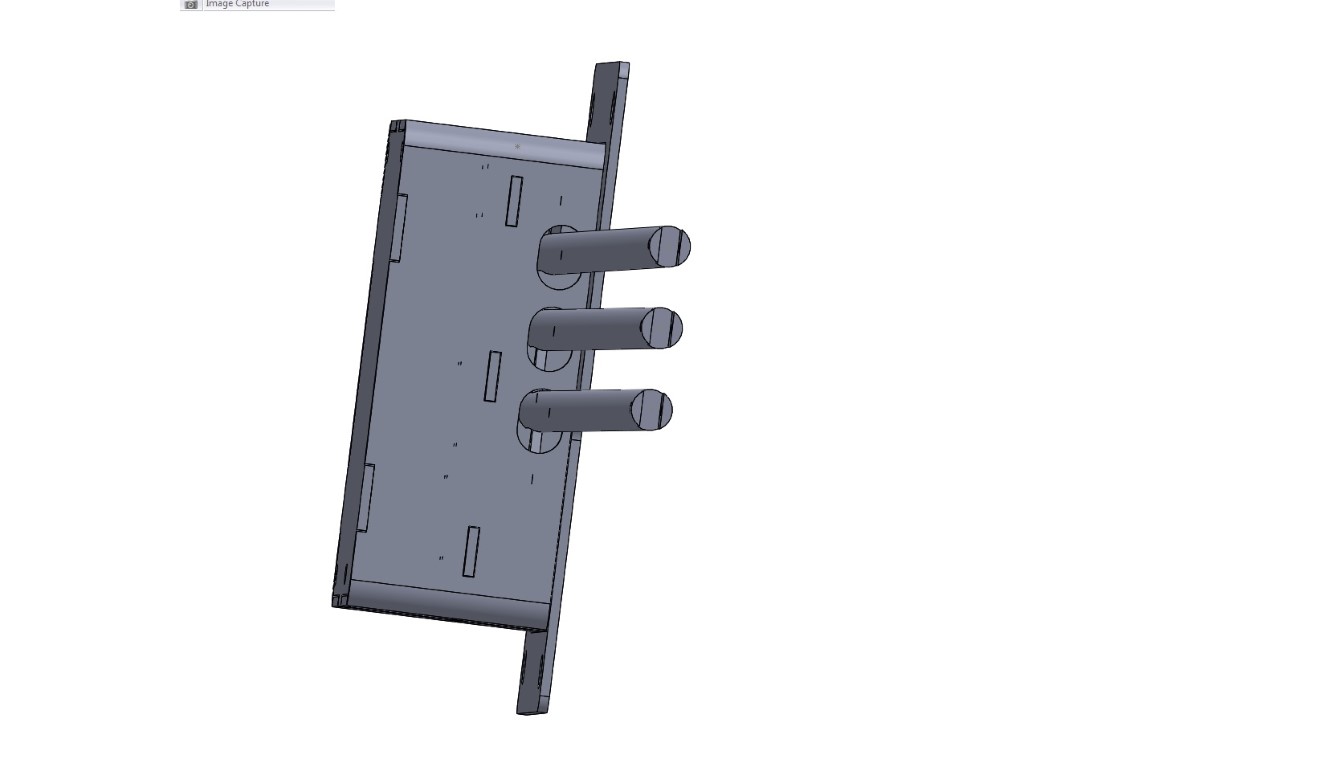
For those interested, the idea is to use a RC servo control board, coupled to PSP style thumb sticks and RC high torque servos to manipulate the aux and motor mechanical actuators.
The RC servo control board is this one:
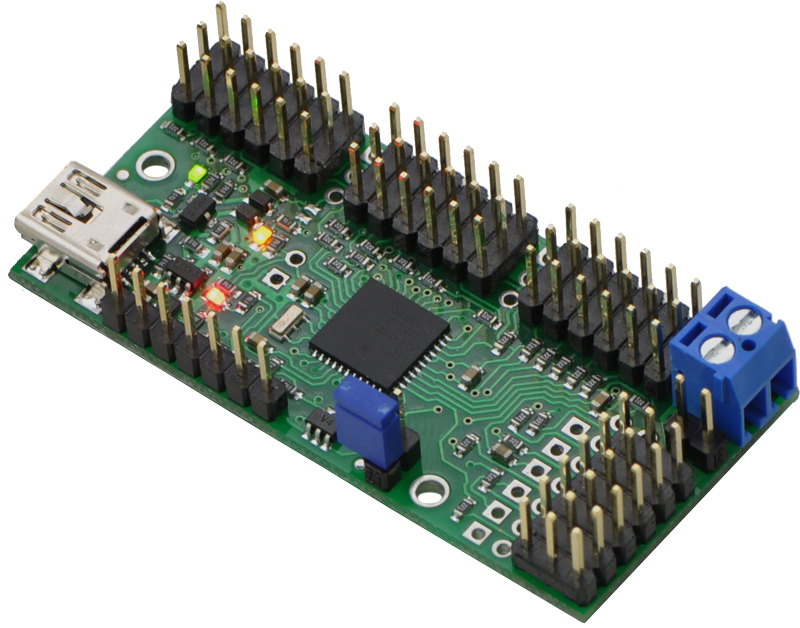
(From the Pololu.com website)
Basically, this little thing outputs a RC servo command based on either direct computer input, or some manipulated electronic input.
So here are the steel parts as received from the laser, plus test fitting the servos:
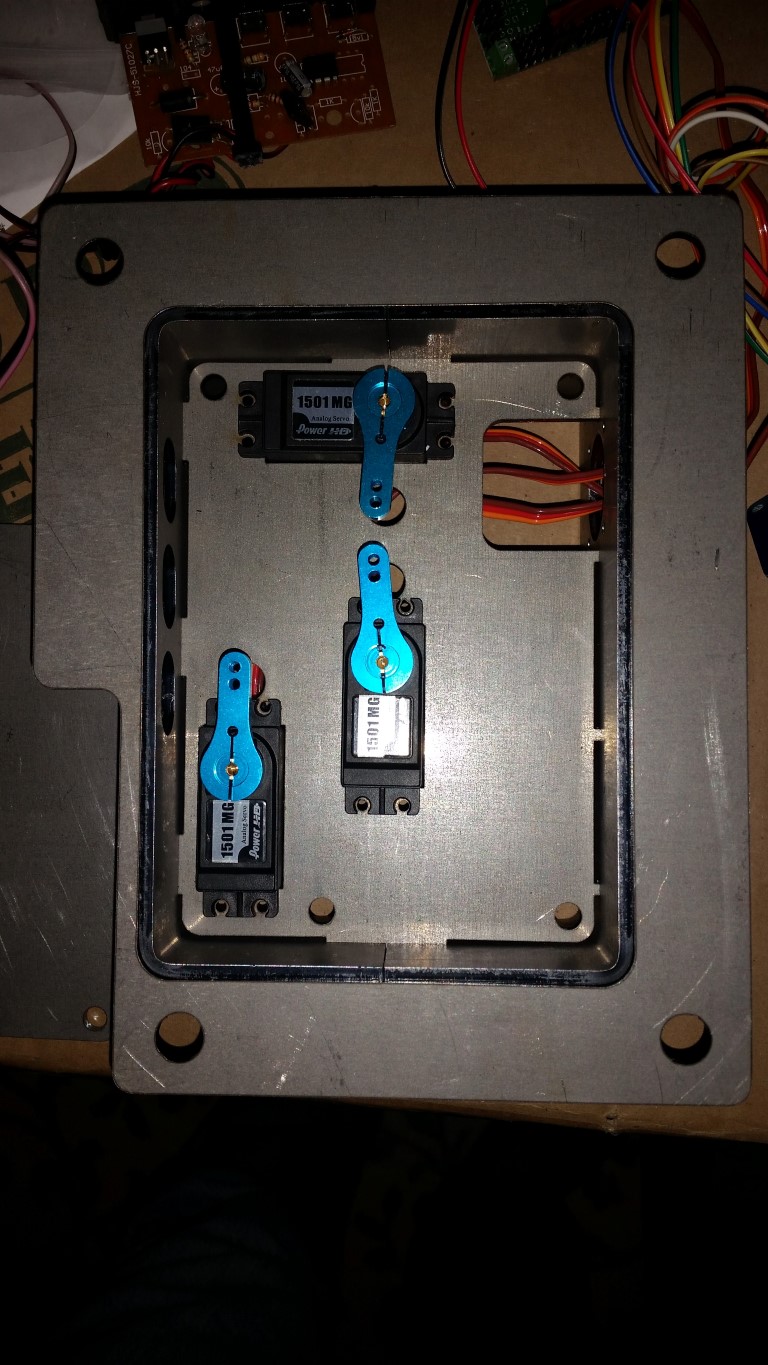
This photo includes the thumb controllers:
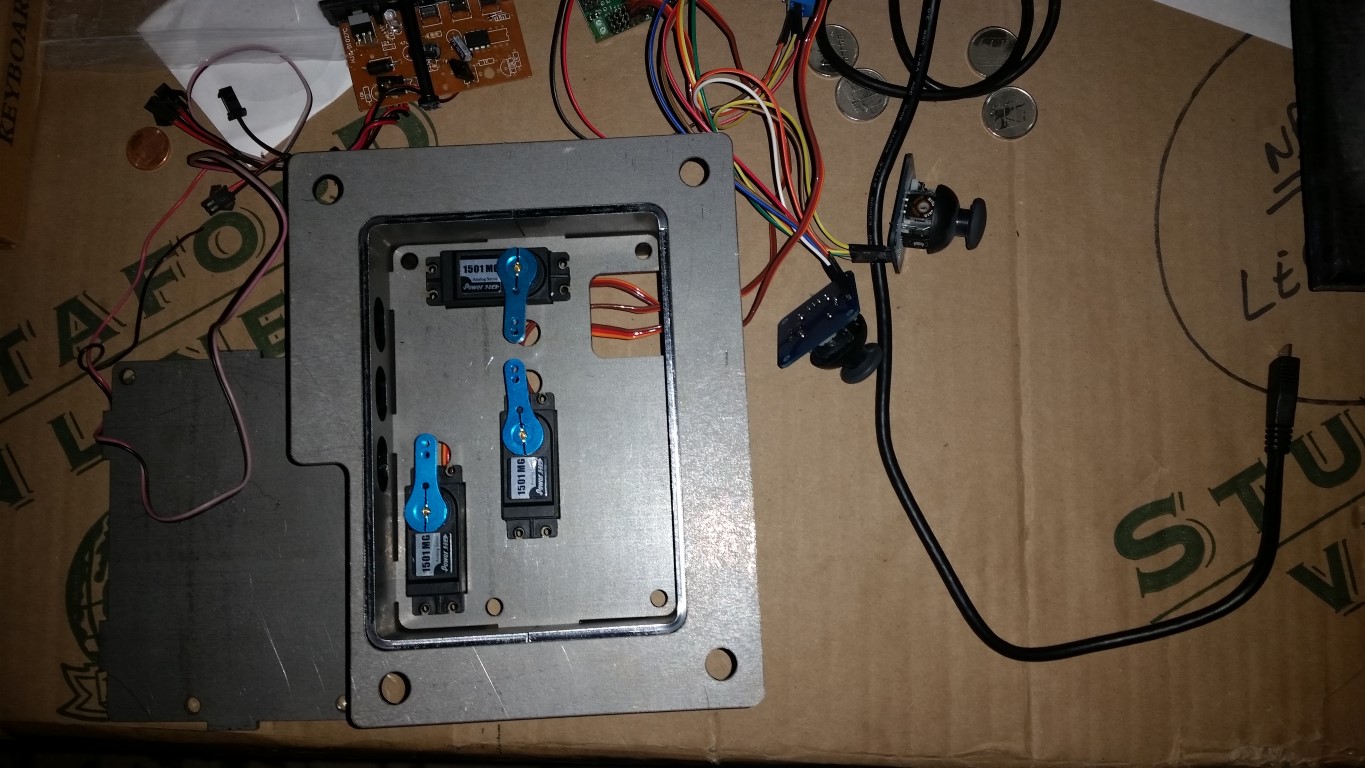
Ok, so I dawdled off to the office to TIG in the various nuts and tap the various holes:
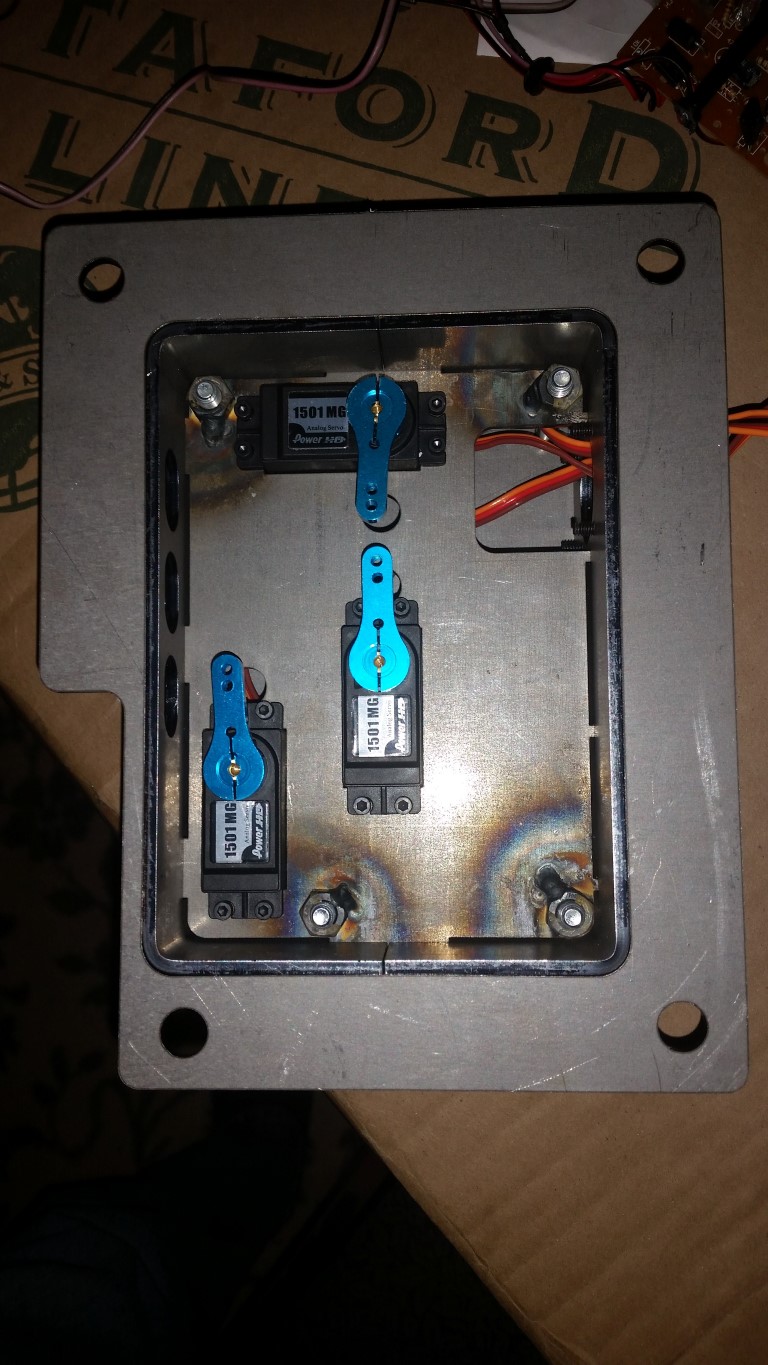
I spent a lot of time finding models for the servos to plonk into my box model. Unfortunately for me, I spent less time on the servo arm models and thought that my approximation of their size would do.
Assumption is the mother of all f ups, so this is the result of the assumption:
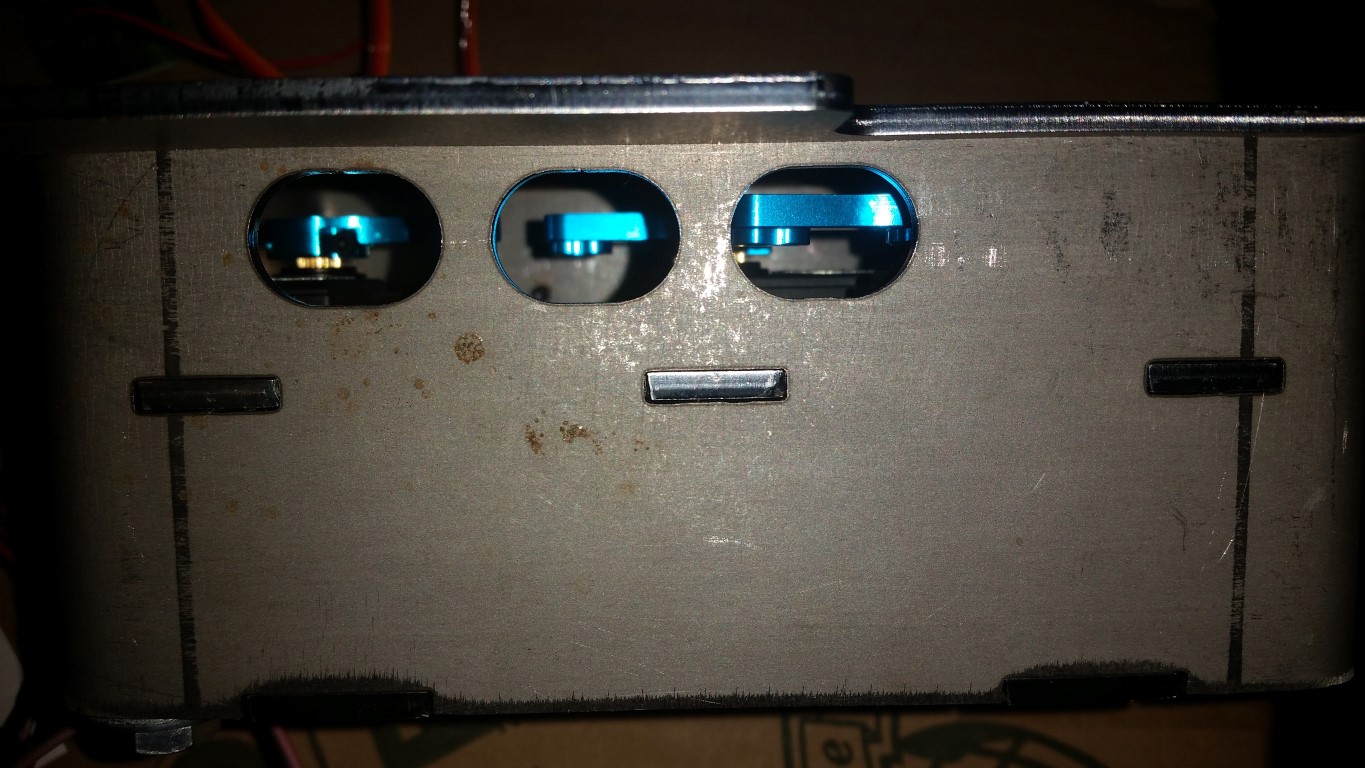
I have a couple of options to get the push/pull rods to be centered in the slots, but it is not looking good for a generic solution.
In my defense, this whole thing is designed to be able to fit into the space of the manual control arms and require zero modifications the little machine, except drilling of some holes.
Don't expect regular updates on this post. This is going to require quite a lot of experimentation and trial and error, but the purpose of posting was to encourage my progress,