I was so pleased with thyself...haha...at being able to replace the bushings without it turning into a dog day afternoon, or having a pro come in and do it...$$$$ My front end rattled like a can of pennies, so I bucked up and got $800 in pins, seals and bushings...which reminds me to get that lathe everybody yaps about and make my own pins. The key was how to get out those bushings, which most likely, were OEM. After googling and googling my dad, I pulled out the MIG and gave it a go. By welding beads in the bushing, it shrinks it a tiny amount. It takes a lot of nerve, in my book, to bead weld the bushings...if I screw this up....burn through was a worry amongst other things, like welding it to the arm, so it never comes off...lol. Anyways, thought I'd post a pic of the crappy bead/spot welds I did...turns out you can suck at welding and it still works. I put four beads approx equal distance apart inside the bushing (noticed I had to crank up the settings on MIG to get a bead laid). I used a wet rag to keep the arm/link cool after each weld. Once done welding, I took the old pin and used it as a punch. On successive bushings, the pin face had flatten out a bit, which made punching out the bushings easier, as the pin got stuck in the bushing. Didn't take all that much effort. Most importantly, no damage to the arm or link. Used 600grit to prep the holes for the new bushings. To put the new ones in, I threw them in the freezer for a day. Then gently tapped them in without any fuss.
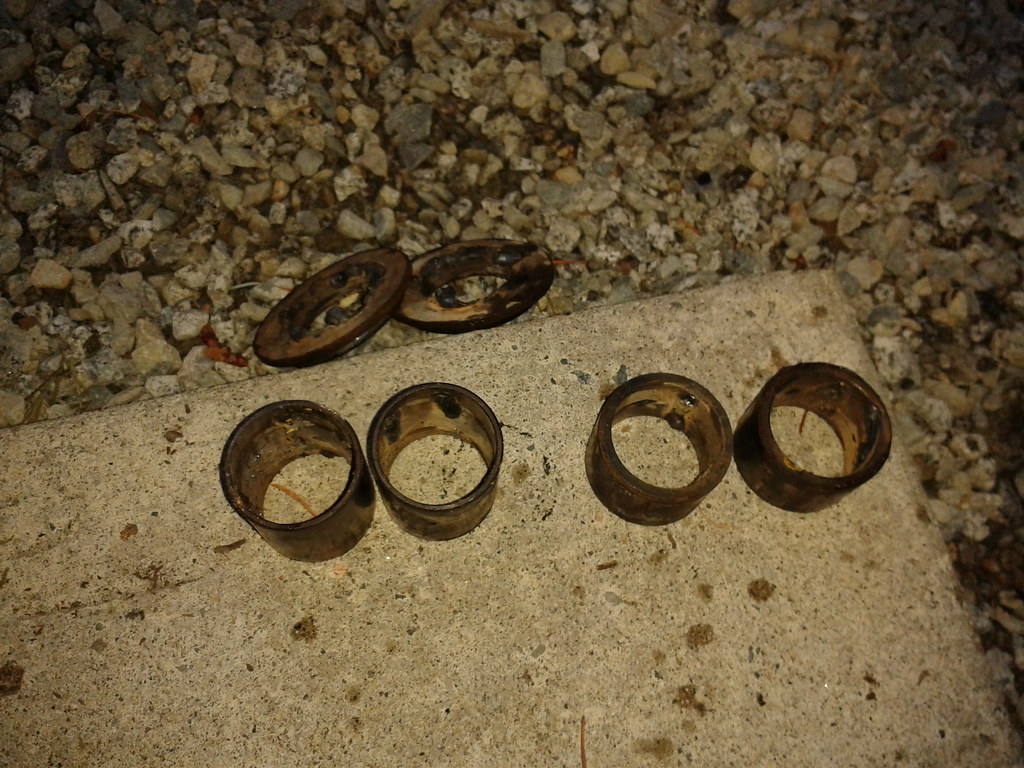

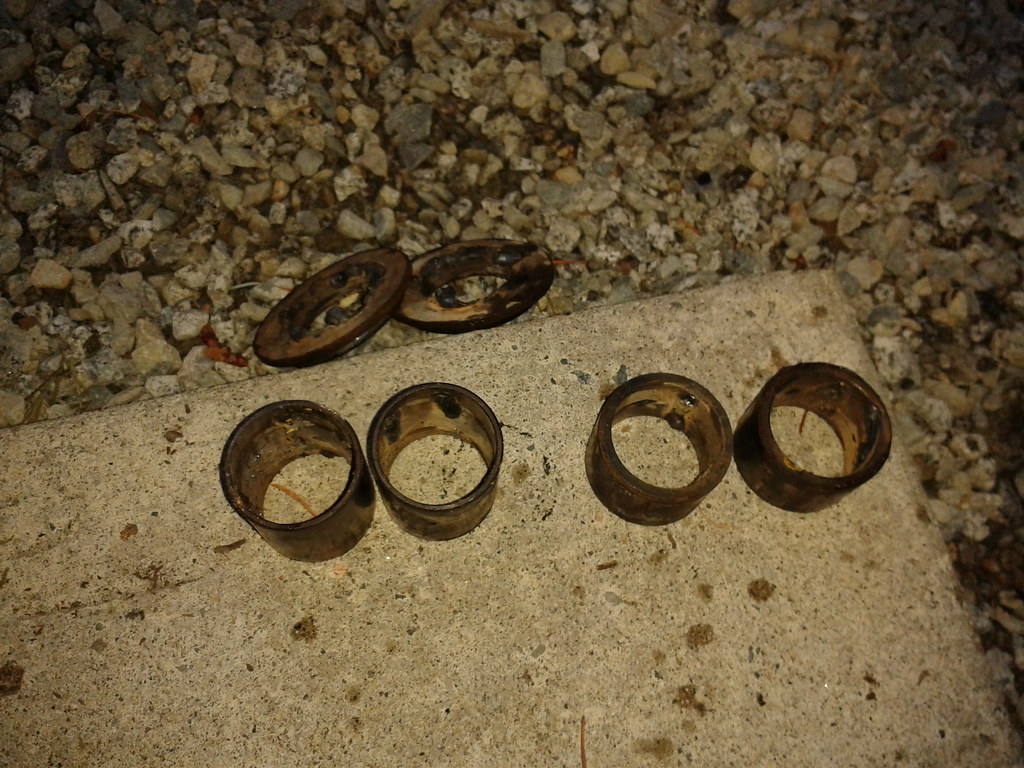